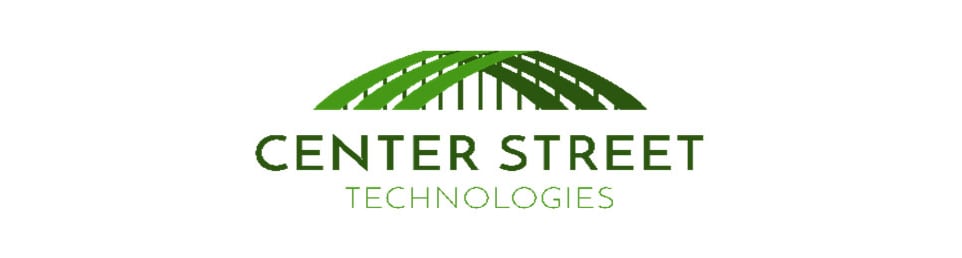
Center Street Technologies: The pursuit of integrating Hybrid Manufacturing with Water-soluble polymers
Hybrid manufacturing combines additive manufacturing (3D Printing) with subtractive manufacturing (5-axis machining) and inspection processes within a single platform. This approach improves production efficiency, speed, and machine utilization by integrating design and manufacturing processes in one environment.
Leveraging water soluble polymers
Manufacturers have started to recognize the capabilities of 3D printing in producing robust and lightweight components and systems. In the recent years it is steadily finding applications for functional parts in aerospace, automotive, railways and construction.
These applications contain complex, intricate geometries and components that often incorporate bridges or overhangs that require support during the printing process. These support structures are separate from the actual model and must be eliminated post-printing. The post processing stage directly impacts the final surface quality, strength, and color of the printed part. This involves using of potentially harmful chemicals, posing risks to the model's surface integrity, and can potentially affect overall quality of the part.
In recent years, a new family of water-soluble polymers have been developed. These polymers can be removed with water, leaving behind the final functional part with a reduced risk of compromising its surface integrity.
Large format 3D Printing at the core
Center Street Technologies (CST), a company based in the USA, has placed 3D printing at the core of their in-house hybrid manufacturing system for applications such as prototypes, sacrificial molds, tools, etc. The ability to produce parts rapidly and efficiently, while eliminating intermediate steps makes the overall process more cost-effective.
In our conversation with Bala K Cherukuri, Senior Project Manager and Robert Berardino, Principal Engineer, we captured detailed insights about how they are challenging the status quo of the industry with their inhouse hybrid manufacturing system.
"At Center Street Technologies, we have developed a large-scale hybrid polymer manufacturing system with a build volume of 2.44 m x 3.66 m x 7.32 m utilizing additive manufacturing, in-situ geometric scanning, and five-axis machining capabilities all within one machine. CST has developed a process known as Advanced Manufacturing Confluence (AMC) that integrates advanced modeling and simulation, application design & engineering, materials science, and industrial controls & automation. AMC allows us to seamlessly perform these operations within one platform, enabling rapid production and quality assessments of sophisticated, large-scale, high-value projects. A single, seamless platform eliminates the need for intermediate steps, making the overall process more cost-effective and reduces lead times," explained Bala.
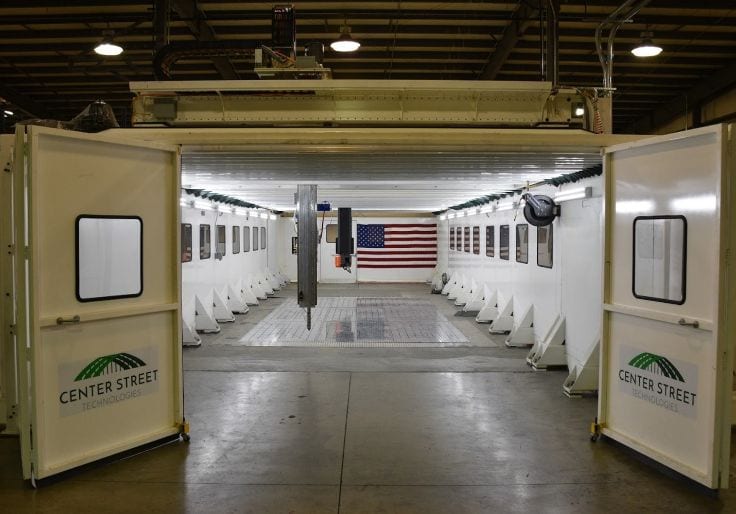
"Our innovation was driven by the necessity to efficiently produce and deliver sophisticated, high-value products on a massive scale for the the Department of Defense (DoD) and aerospace customers. To better serve this market, we focused on developing a digital thread approach that streamlined production, monitoring, and optimization of our advanced hybrid manufacturing capability," explained Robert.
Their AMC system provides a comprehensive process flow from customer requirements, through design to final part shipment. The set up aims to successfully leverage the strengths of water soluble polymers and hybrid manufacturing. The system uses a Model-Based Definition (MBD) approach (an approach for creating 3D models that effectively contain all the data needed to define a product), that enables a reliable digital definition of a product in the 3D master model. This approach drives both the additive/subtractive manufacturing processes of the AMC system and provides the baseline for the in-situ 3D laser scanned “as-manufactured” digital twin.
"Our hybrid 3D printer, custom-designed and operational since 2017, has been pivotal in expanding our capabilities. We're constantly pushing boundaries, exploring materials like carbon fiber ABS and Polyether Sulfone to meet diverse manufacturing needs.", elaborated Robert, who is leading the materials development at Center Street Technologies.
Integrating best of both technologies
"The current approach we're exploring involves experimenting with manufacture of hollow structures with complex geometries for large-scale parts. We believe that water-soluble pellets could be the missing piece of this puzzle.," Robert explained.
CST plans to scale up its operations and expand their market presence by incorporating water-soluble pellets as support materials into its portfolio. This would also further upgrade the value proposition of serving the aerospace and defense industry with more functional parts. CST in collaboration with MCG aims to upgrade their manufacturing capability with a co-material development initiative.
Their hybrid manufacturing system represents a paradigm shift in additive manufacturing. "We're not just creating parts; we're redefining possibilities. Through collaboration and innovation, we are aiming to upgrade the future of manufacturing, one breakthrough at a time," concluded Bala.
For more information on their technology visit https://centerstreettech.com/
The Center Street Technology team was conferred with a Special Recognition by the jury team of the 3D Printing FGF Engineering Challenge for their pursuit of advancing and challenging the status quo of 3D Printing FGF.