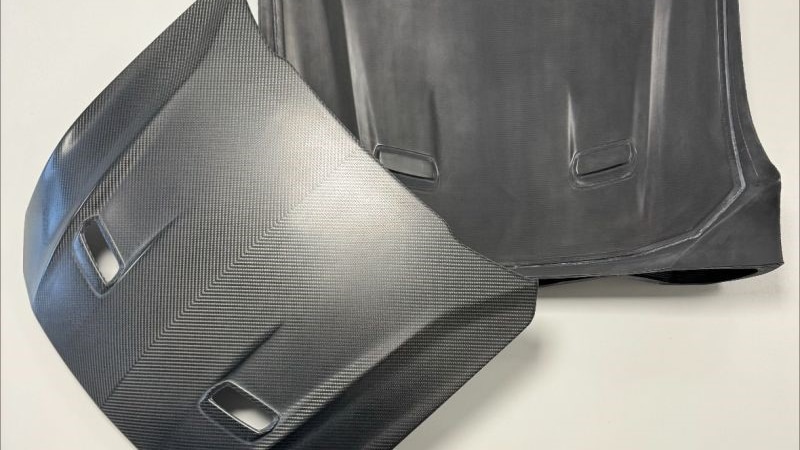
Dash CAE: Shaping the future of sustainable composite mold manufacturing
In today's rapidly evolving manufacturing landscape, carbon fiber reinforced polymers or composites play a pivotal role in industries, such as aerospace to automotive. However, traditional manufacturing methods pose significant challenges such as high costs, lengthy production times, and material waste. These factors serve as roadblocks to further innovations and constrain the possibilities of adopting composites.
Carbon fiber-reinforced composites offer a strong blend of properties and provide distinct benefits, making them ideal substitutes for many materials. In recent years composites have experienced a surge in demand which has subsequently lead to an increase in waste generation. With future regulations expected to prohibit landfill and incineration disposal methods for composite waste, finding alternative solutions, such as recycling, is becoming seemingly important.
Dash CAE, an advanced engineering company pioneering applications with composites have identified the challenges of recycling composite molds and are on the journey towards solving this issue. Our conversation with Ryan Muller , the Sales director at Dash CAE provided us with comprehensive insights into their solutions and how they intend to sustainably innovate in the design and production of composite parts.
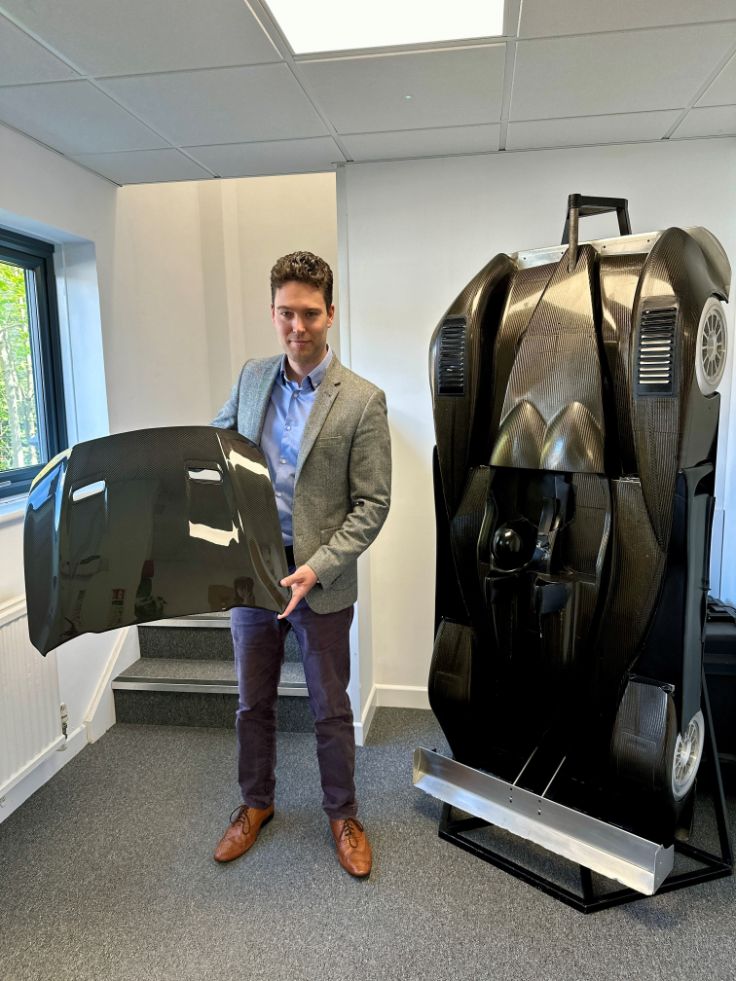
"Dash's journey started as a design and structural engineering company, specializing in wind tunnel models and analysis work in static linear and dynamic non-linear analysis software. Over time, we have expanded our capabilities to manufacturing of parts and have fully vertical integrated comprehensive services from design to manufacturing, including in-house tooling," explained Ryan.
Dash CAE has since developed its capability by serving specialized applications in markets such as F1 motorsports, automotive, space and defense, and marine. They have built on their capability by providing a comprehensive engineering toolbox, from designing on software and rapid prototyping to tooling with additive manufacturing and advanced composite part production.
Sustainable lifecycle of molds
Dash's proposal addresses the issues with molds due to the presence of bond lines when using traditional methods. Bond lines refer to the areas where different layers of tooling board are joined together using adhesive. They can be detrimental to the part quality due to differences in hardness when hand finishing causing (zebra stripes) and can even be susceptible to failure. Shallow machining angles through bond lines can also cause large patches of adhesive witnessing through to the surface, causing unsightly distortions.
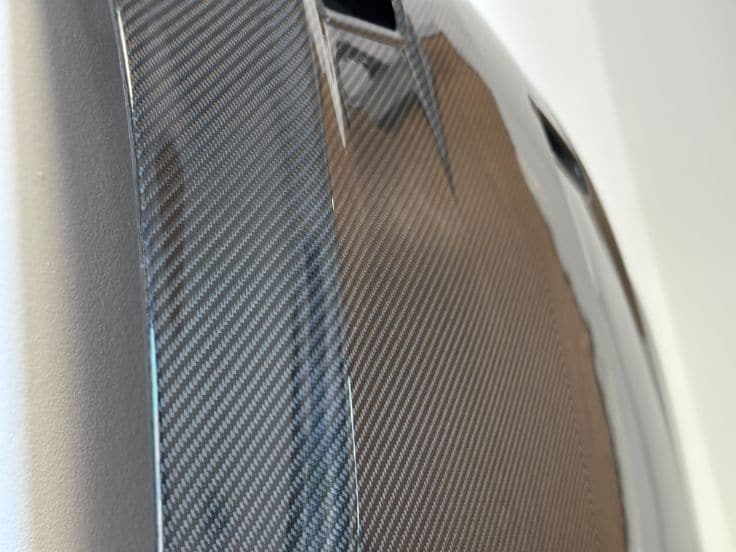
"We are analyzing various business models that would preserve quality while ensuring sustainability. Moving ahead, we would like to offer some unique propositions to customers with a commercial agreement for recycling the molds. Let's say a customer needs to revise the design of their mold. It would be a game-changer if we could take the mold back, recycle it, and manufacture a new mold with the recycled material. The customer would end up paying much less since they have already paid for the material," continued Ryan.
Ryan and the team at Dash are exploring ways to collaborate with recycling companies that would collect the molds from the customer at the end of their life and use the recycled material for future designs to close the loop. This would also significantly reduce the lead time for the mold.
They have also started to experiment with robot 3D Printing as an upcoming technology for manufacturing large-scale components for marine and aerospace applications.

"We intend to leverage the capability of our in-house robot extruder to utilize different variants of material for the molds. We believe in the potential of 3D printed molds as they often outperform carbon molds. Some of our molds in service have completed 250 manufacturing cycles, which is exceptional considering that typically, we expect around 80 to 100 cycles from a carbon mold. This could be a game-changer for applications as it also significantly reduces manufacturing costs," highlighted Ryan.
The path ahead
Dash has identified significant benefits of incorporating 3D Printing with pellets into their production process. Apart from enhancing recyclability and reducing lead times, the incorporation of hybrid composite manufacturing technologies for mold manufacturing has a high potential for further improving part performance for various industries.
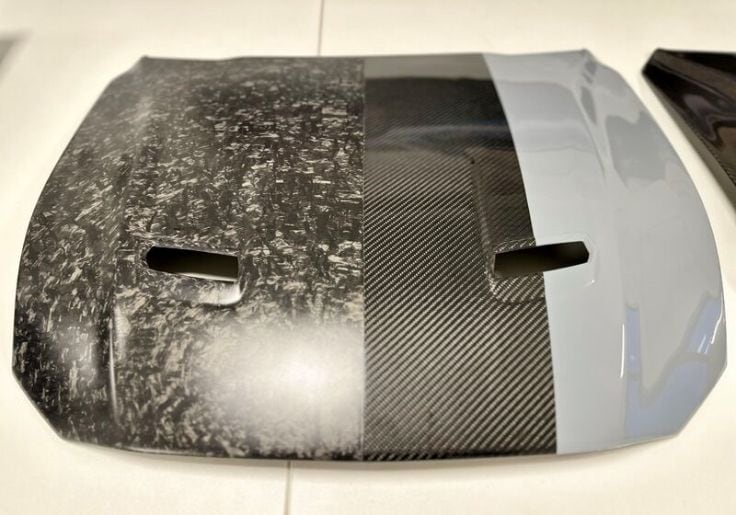
"We are further fine-tuning stiffness testing and machining strategies to optimize surface quality and achieve superior rigidity and vibration reduction in our future molds. This would require meticulous attention to detail in post-processing and testing to deliver top-tier results consistently," concluded Ryan.
Dash CAE was one of the Finalists in the 3D Printing FGF Engineering Challenge. The jury team was impressed with their pursuit of recycling composite molds to lower their carbon footprint and promoting the benefits of large format 3D Printing.