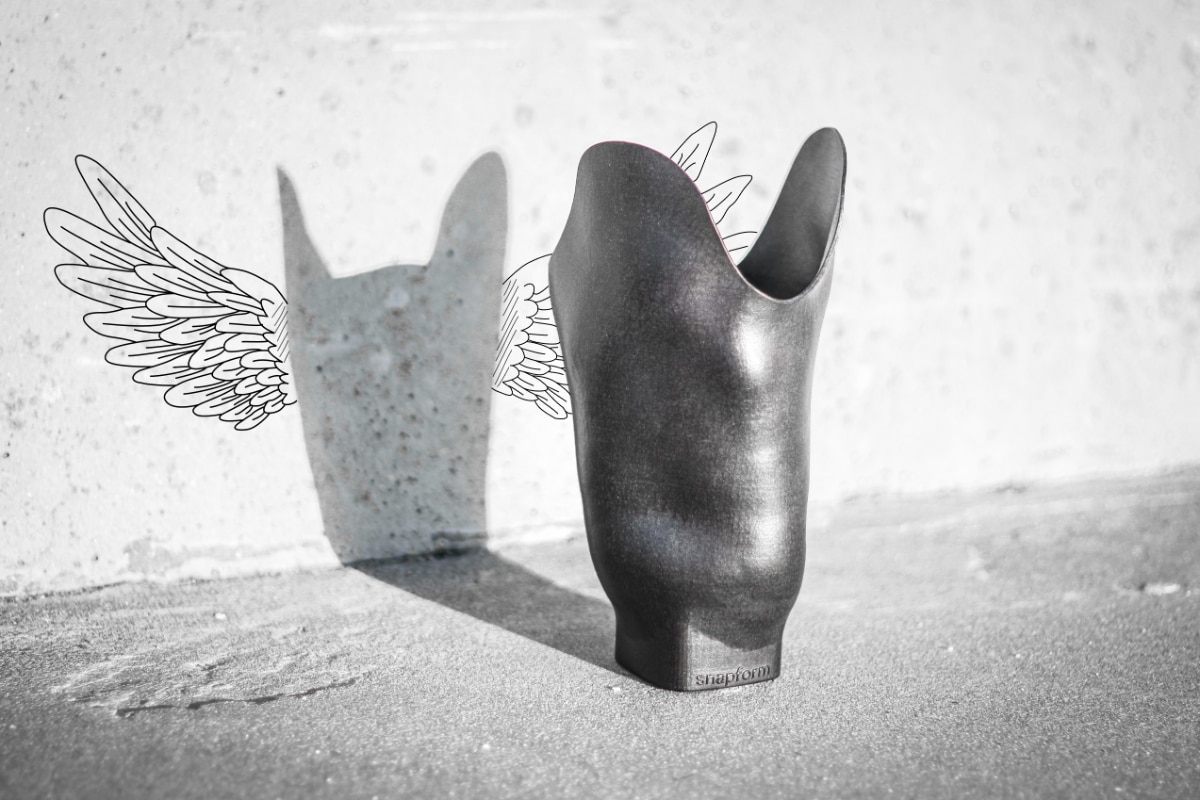
Data-driven socket design: Snapform's pursuit of making prosthetics accessible
Prosthetic limbs serves as a replacement for a lost arm or leg and enable individuals to carry out everyday tasks such as dressing, eating, and walking - facilitating an independent life. Prosthetics have evolved substantially over the years, allowing many users to regain a level of mobility comparable to their pre-amputation state.
However, the effectiveness of a prosthetic device depends greatly on its fit. Poorly fitted prostheses can lead to discomfort, sores, blisters, and an increased risk of falls or accidents. They can significantly exacerbate the challenges faced by wearers in performing their daily routines, leading to frustration and a reduced quality of life.
Crafting a prosthetic socket (the custom-fitted component of a prosthesis) requires manual fitting, and patients often need to undergo multiple trial-and-error fitting sessions before achieving a reasonably fitting socket. This process is not only time-consuming and expensive but also burdensome for the patient. Additionally, over 60% of individuals experience issues such as pressure ulcers and skin infections, while 40% report experiencing pain when using the prosthesis.
Andreas Børresen and Martin Gerth Andersen at Snapform are pursuing a shift towards advancing by developing of a new method for creating affordable, tailored prosthetic sockets that fit users perfectly.
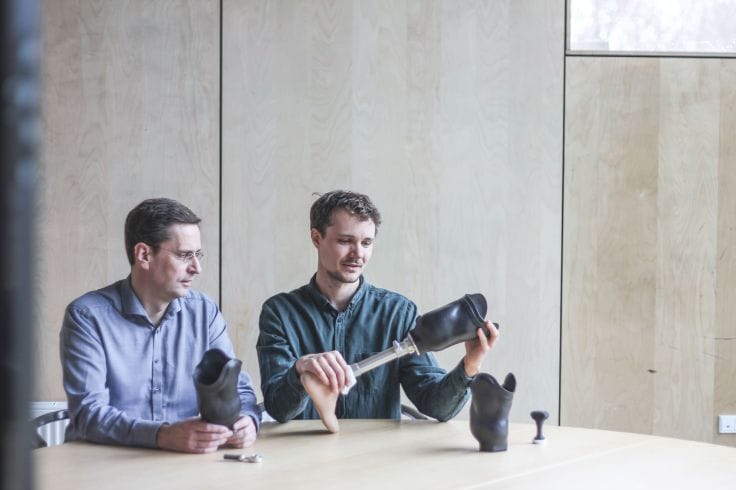
"Prosthetics are essentially divided into two components: a socket, which must be custom-designed and fitted for each patient and a leg that one can buy off the shelf. The socket plays a crucial role in the prosthetic system, as it largely determines the comfort level for the user. Our goal is to ensure that amputees, especially those living in conflict regions, have access to well-fitted prosthetics," explained Martin.
Data driven socket fitting
Snapform has developed a unique solution for designing and creating better-fitting sockets with a scientific and data-driven approach. Their proprietary software, Simfit, combines 3D scanning, printing, and advanced simulation to determine an optimal socket shape. Their software utilizes surface scanning of patients' legs to design perfectly fitting sockets, tailored according to customer requirements.
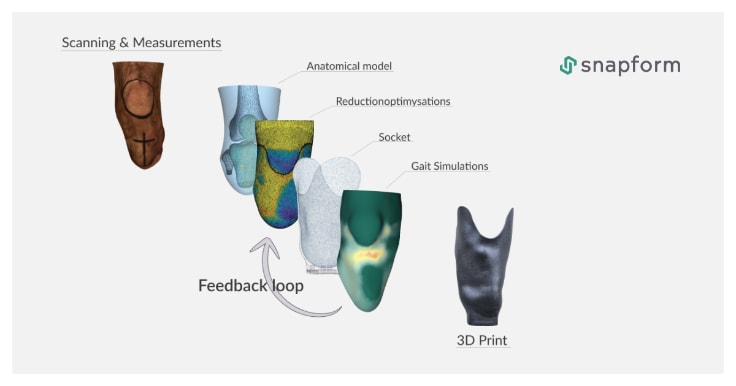
"Our technology eliminates the trial-and-error fitting process, which is costly and time-intensive. As a result, the total design and manufacturing costs of a socket are reduced by 60%. Our process is streamlined as it eliminates the need for an experienced prosthetist in the fitting process. This saves valuable time and resources while improving patient comfort," highlighted Martin.
How it works
Snapform has defined a streamlined process that begins with 3D scans of the leg. The 3D scanner analyzes and measures the geometry of the stump (amputated limb). The software generates a 3D simulation and defines a geometry based on predefined parameters.

Once the shape is computed with a proper finite element analysis, it creates virtual simulations of the sockets in operation. This helps perfect the final part without the need to manufacture several iterations of the socket.
"Many amputees lose their limbs due to diabetes and its associated complications. This results in reduced sensation in their feet and legs (neuropathy), posing challenges for amputees to provide feedback on the prosthesis fit. Prosthetists have to rely on intuition and experience when shaping the prosthesis. Our solution eliminates the need to work with intuition and leverages data to ensure a good quality socket that fits perfectly in the first try," Martin explained.
Leveraging the benefits of additive manufacturing
Snapform combines mature technologies such as 3D scanning and printing with advanced simulation technology to determine the optimal socket shape. As 3D scanners become more affordable, Snapform's simulation software eliminates manual components of manufacturing. Their goal is to find a cheap, reliable, and agile production technique that would optimally serve the users.
They have identified 3D Printing FGF as a game-changer in the prosthetics industry. In the future, Snapform intends to combine FGF with carbon fiber and other hybrid composite technologies to further enhance the strength and durability of their prosthetic sockets.
"Our goal is to manufacture properly fitting, customized and affordable prosthetics accessible to patients in regions affected by conflicts, wars and those without access to affordable assistive technologies. We believe that additive manufacturing is the piece of the puzzle that would enable a pursuit towards a faster, more sustainable and better fitting prosthetics for everyone," concluded Martin.