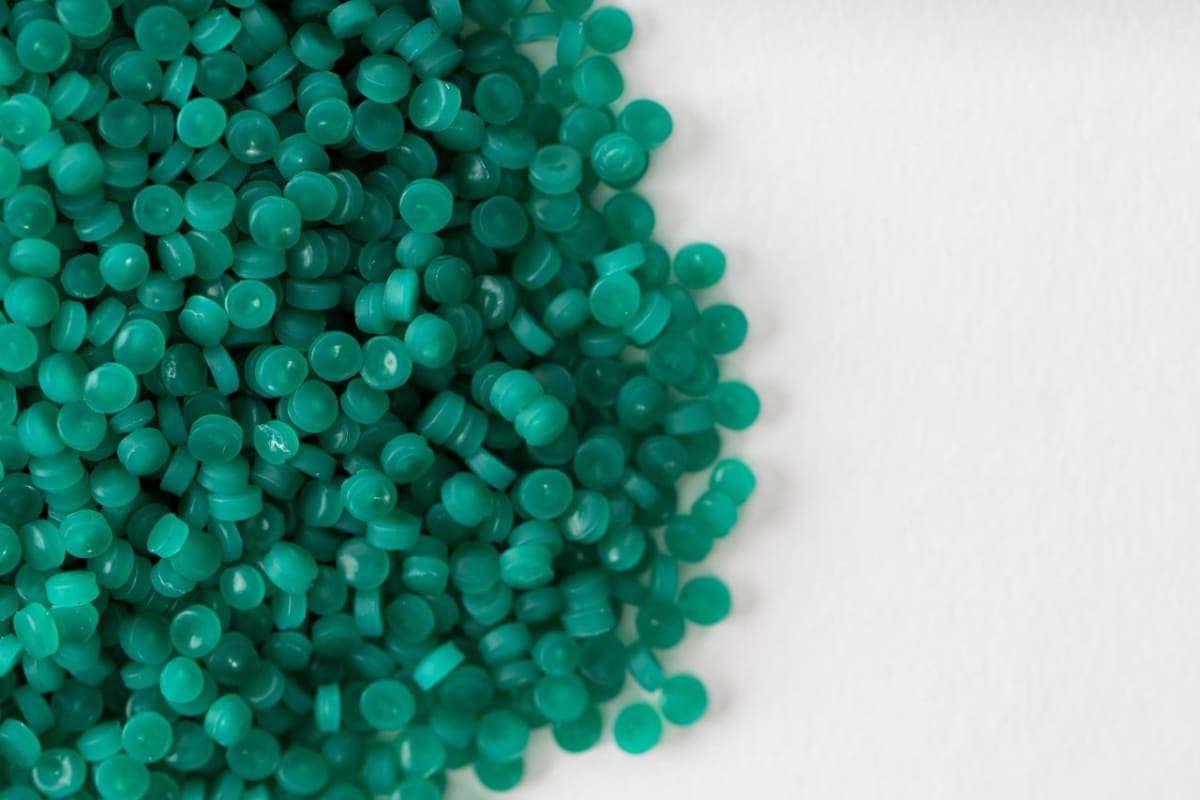
Transforming Marine and Agriculture Plastic Waste
The threat from plastic pollution has escalated from a minor environmental concern to a full-blown planetary crisis. Since the World War 2, plastic production has grown on an exponential scale.
To put it into perspective, half of all the plastic ever produced was between 2003 and 2016. In 2016, it was estimated that there was ~23 million tons of plastic waste in the ocean.
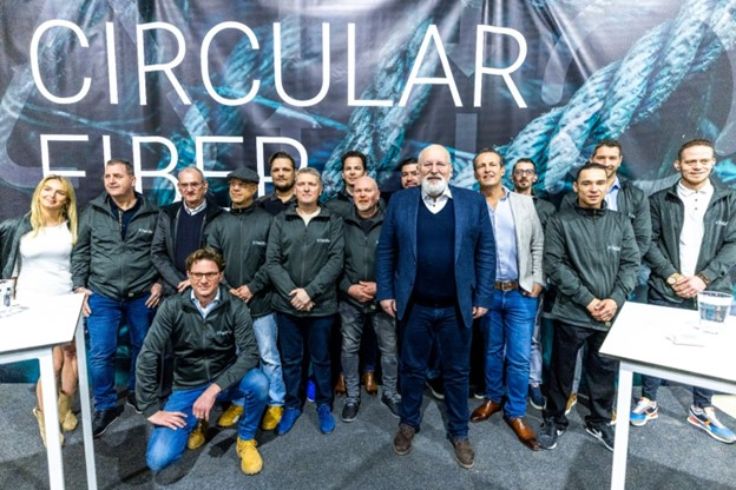
HEALIX, a Dutch startup has identified this crisis and has pledged to tackle the issue by focusing on plastic fiber waste from two sources: The agriculture and maritime industry. In our conversation with Sjoerdje Meijers (marketing and communication lead), we got a comprehensive overview of how HEALIX is tackling this important environmental issue.
Circular future for plastic fiber waste
"Plastic waste in oceans is increasing at a rate of 11 million metric tons a year and is extremely debilitating for marine life. Without immediate action, the amount of plastic will triple by 2040. To make matters worse, there could be more plastic than fish in the ocean by 2050. At HEALIX, we have identified the urgency and are aiming to make plastic fiber waste circular," explained Sjoerdje.
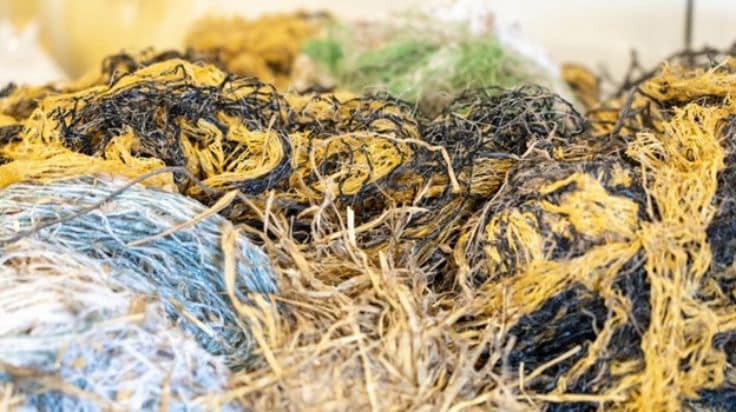
With their proprietary technology, HEALIX is transforming discarded nets and ropes from fishing and farming into recycled polymers (HDPE & PP) for the global manufacturing supply chain. The recycled polymers can be reused for extrusion or injection molding of new applications.
What does the process look like?
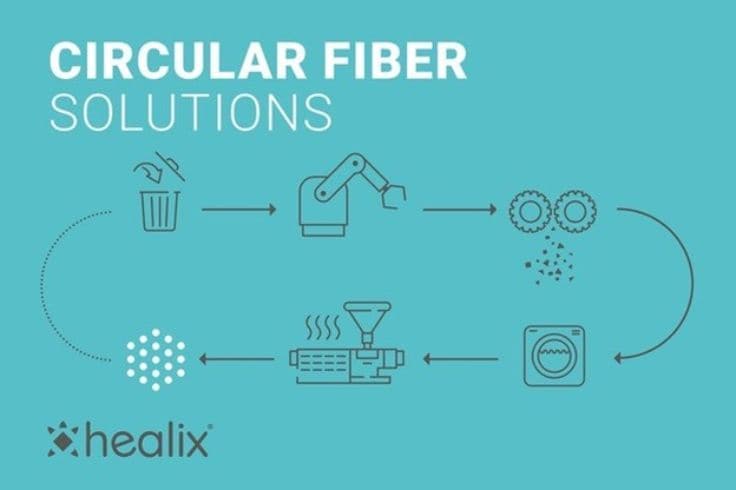
"The steps in the recycling process are quite interesting. Used twines, ropes, nets, and other plastic fiber waste is collected, sorted, shredded, washed, and reprocessed into recycled polymers with virgin like quality," elaborated Sjoerdje.
The process is divided into three phases: Preparation, Cleaning and Extrusion.
1) Preparation
"Consumer waste from marine and agriculture is always contaminated with organic waste and requires pre-cleaning and sorting before it enters the shredder. Sorting and separation of plastics (HDPE and PP) is carried out by our reliable external partners," continued Sjoerdje. Pre-cleaning is an important step as it eliminates contaminants, which if left behind would compromise the structural integrity of the recycled polymer.
The collected waste is stored in bales and requires sorting, chopping, and shredding in a chopper to facilitate a continuous, homogenous feed. This step allows for inspection of contents entering the recycling process.
2) Cleaning
The sorted, chopped and pre cleaned material is sent to the cleaning section of the process. In this step, the objective is to remove all organic and inorganic contaminants fixed and trapped on the plastic waste. "We try to minimize resource usage by purifying used water and reusing it, to push it back into a closed loop. In case of materials with thin diameters, there is a high likelihood of particles being trapped inside individual filaments. The plastic fibers must be mechanically washed and further chopped, so that particles that are stuck in it are released," explained Sjoerdje.
3) Pellet extrusion
In the next step, cleaned fibers are fed into an extruder barrel. A screw extruder gradually melts the material, is degassed, and subsequently forced into a pelletizer. Once cooled, the material is left behind is in form of pellets. “Our customers usually prefer the final material in form of small pellets over long semi-continuous extrusions as they are easy to transport,” Sjoerdje clarified.
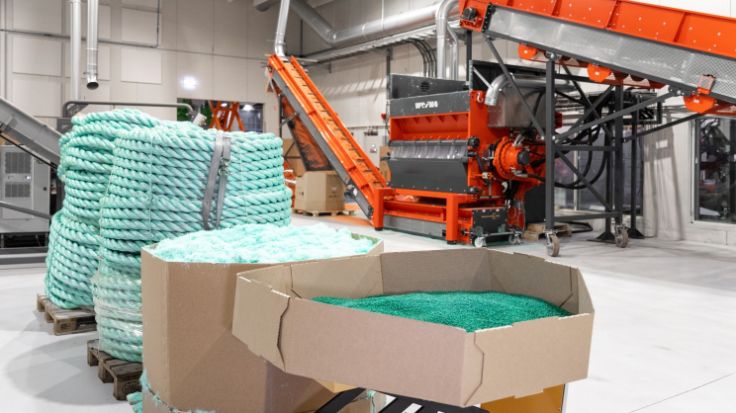
Sorting is an important step in this process to avoid contamination with other plastics as only HDPE and PP can be recycled at present.
Extending beyond marine waste
Healix’s foundation was based on tackling marine plastic waste and on their journey towards making the oceans plastics free, they identified other areas of focus. Agriculture is an industry which is heavily plastic dependent and contributes to significant amount of plastic waste in farmlands.
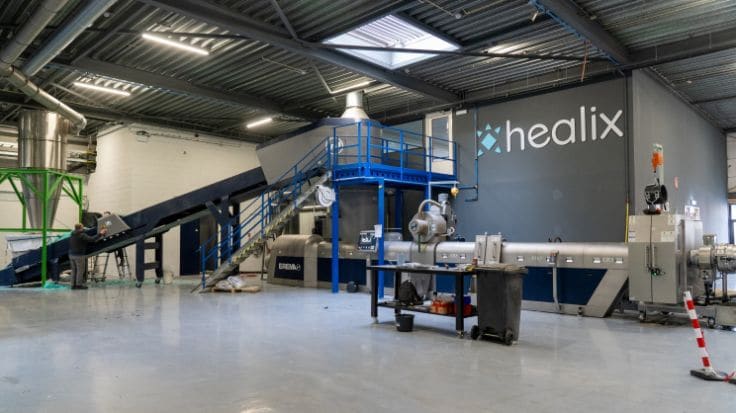
"Around 12.5 million tons of plastic products are used for agriculture in Europe every year. This generates significant waste and requires immediate attention, before it gets out of control," Sjoerdje pointed out. Healix is currently working with agriculture suppliers and have developed a closed loop recycling system for waste baler twines (synthetic twines used to bind fibrous material like hay or straw, made from polypropylene).
With a recycling facility already setup and plans to expand even further, Healix is well-prepared to tackle the rising plastic fiber pollution issue.