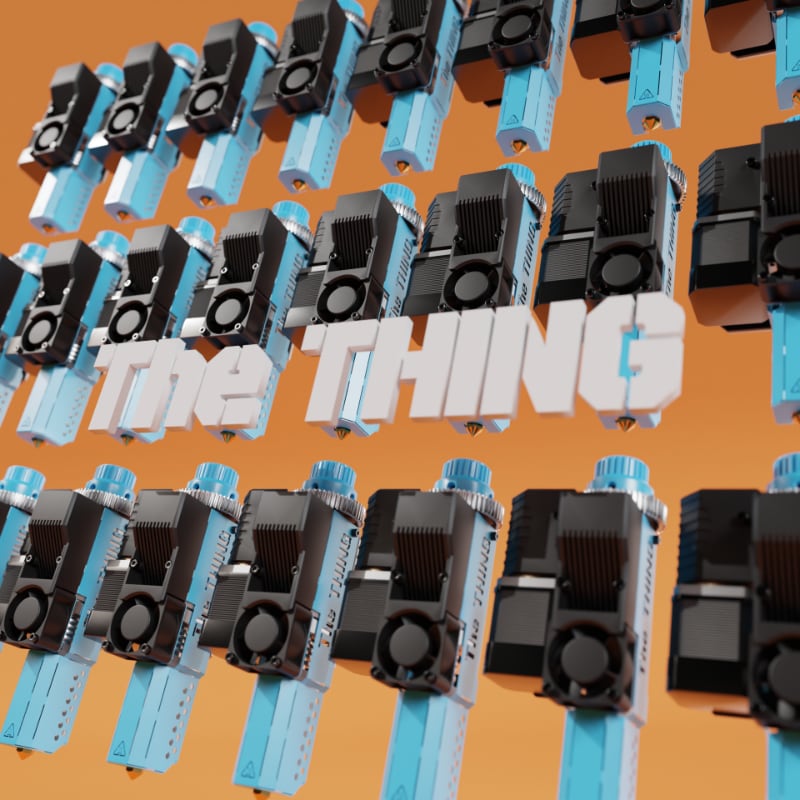
Helix's "The Thing": Paving the way for an accelerated adoption of 3D Printing with pellets
Fused Granulate Fabrication (FGF) is an extrusion-based 3D printing method using plastics or composites granulates. It melts and extrudes plastic pellets, layer by layer, allowing intricate and customized object creation. FGF's versatility in utilizing a wide-range of plastic and composite granulates makes it cost-effective, scalable, and suitable technology for several applications.
In its current state, Fused Deposition Modelling or 3D Printing with Filaments is the most widespread 3D Printing technology. However, with the emergence of various FGF extrusion systems and hundreds of grades of customizable plastic granules suitable for 3D printing businesses, researchers and 3D printing aficionados are pursuing the use of this wide range of materials through FGF technology.
Filip Turzynski at his company Helix is on a path to enable users to tap into the full range of different 3D Printing materials with their universal FGF extrusion system.
"For over 8 years, I was working as a 3D Printing R&D manager at a printer manufacturing company. During this time I was in contact with many material suppliers and printing technologies. I soon realized that there are so many more different materials that can be used for 3D printing outside of what is currently available in filament format. Oftentimes these materials simply can’t be made into filament. Hundreds of different plastic grades with highly functional properties or coming from recycled sources should have a proper technology that do them justice," started Filip.
The 'Eureka' moment
This was the moment when Filip narrowed his focus towards 3D Printing FGF, as it enables printing with virtually any grade of plastic. The next step in the pursuit to enable a broader audience to use FGF was to find ways to retrofit existing desktop printers with extruders.
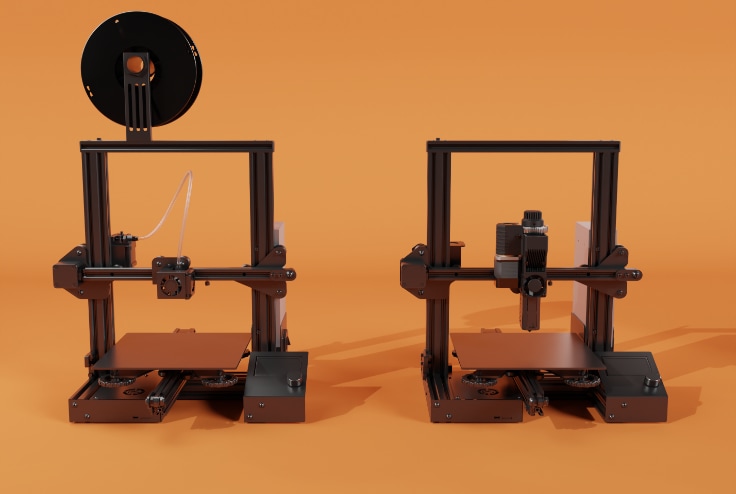
"After years of working in the field, I realized that 3D Printing is basically like a “sophisticated hammer”. It is a tool, which, if used with a proper material and application has the potential to unlock several new possibilities, bringing cost effectiveness, accelerating research or helping turn waste into interesting new products quickly. At the same time, I came across a paper by Prof. Joshua Pearce where he introduced a screw compression grinding setup," continued Filip.
In 2020. Joshua Pearce, in collaboration with colleague Jacob Franz at Michigan Technological University, developed an open-source grinding machine for compression screw manufacturing. This project enables innovators to produce low-cost 3D Printing extruders that can replicate commercial screws. This inspired Filip to pursue building an extrusion setup that can be retrofitted into most commercially available desktop 3D Printers.
After almost 2 years, Filip has successfully developed the first minimum viable product that has already been tested with a wide range of materials.
Rise of the 'THING'
Filip studied the market and its landscape, and realized that commercially available solution of retrofitting printers for screw extrusion have some limitations. For instance, their screw design is not optimized to accommodate varying pellet sizes and geometries. This results in inadequate diameter of the screw and/or depth of the channel that prevents the equal distribution of material with each rotation, resulting in pressure differences, variable extrusion width, extrusion failure, and motor stalling.
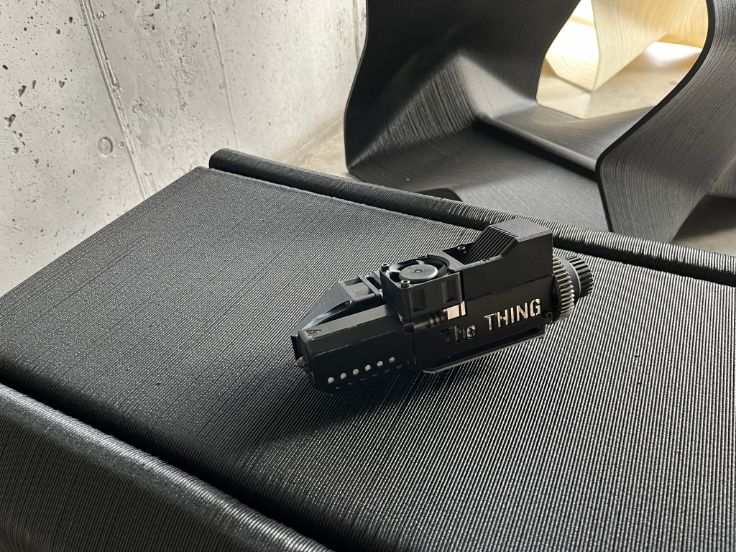
"There are very few FGF extruders compatible with existing 3D printer setups, most of which come preinstalled on printer chassis, increasing entry costs into the technology," claimed Filip.
The pellet extrusion enabler designed by him from scratch, also known as the 'THING', aims to address the aforementioned issues, enabling wider adoption of FGF. Filip has also manufactured the screw for the extrusion setup fully-inhouse. "In order to manufacture unique, custom screws, a dedicated machine was built, and a special piece of software was developed to allow rapid iterations of the screw design by machining the screws out of 15mm stainless steel blanks. This helped me develop a solution based on a combination of screw and funnel geometry with a finer pitch and a relatively high throughput, capable of accommodating and feeding most common pellet sizes and shapes," explained Filip.
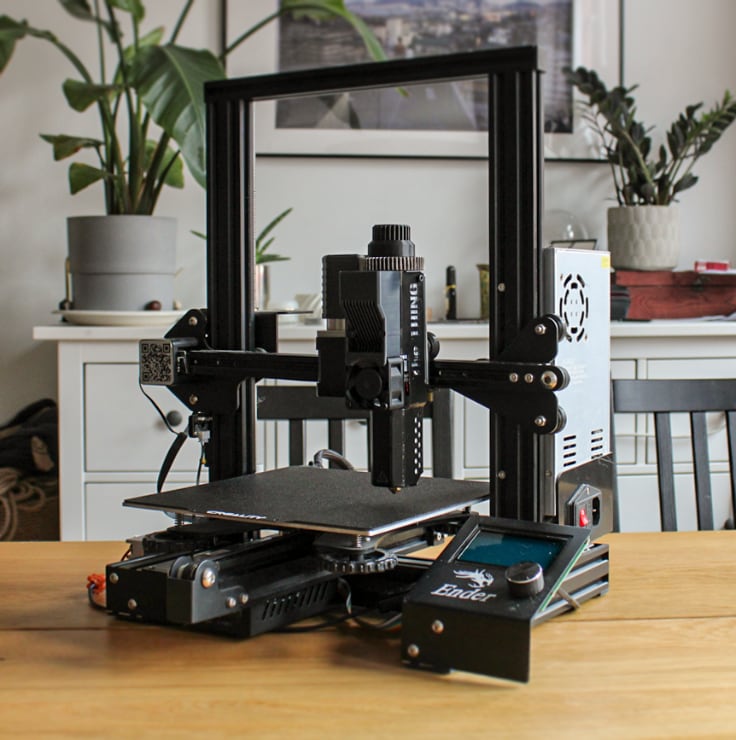
Furthermore, the extruder is driven by a high-torque, high-reduction planetary gear stepper drive, specifically chosen to provide sufficient torque to cut through or push aggregated material.
Scaling up to a broader audience
"I believe that the intrinsic value of FGF extends beyond large-scale parts and encompasses a wide range of possibilities, including those on a smaller scale. FGF's value lies in its ability to empower users to select and print materials according to their preferences. Our product, the 'Thing', serves as the missing piece of the puzzle, as it enables functionalized extrusion for a broader audience," reiterated Filip.
Filip aims to make his extruder as a point of entry for users aiming to adopt FGF for their applications. In order to enable a smooth transition, the setup only requires a set of Allen keys for assembling and was designed to be integrated with standard 3D printer hardware and motherboard PCBs.
This video gives an overview of Helix's innovation and how they intend to enable a wider user base to adopt 3D Printing FGF.
Filip Turzynski at Helix was conferred with a Special Recognition by the jury team of the 3D Printing FGF Engineering Challenge. for their pursuit of advancing and challenging the status quo of 3D Printing FGF.