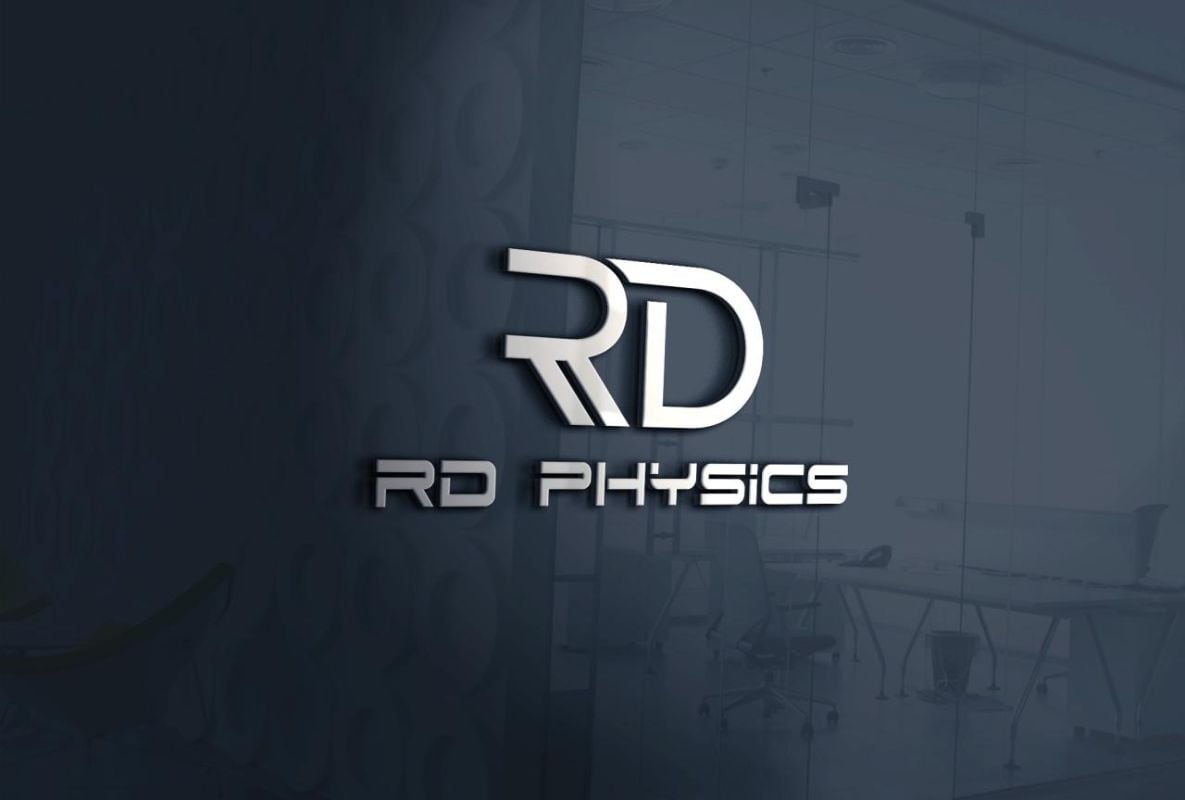
RD Physics
The Circularity Gap report 2021 estimates that just 8.6% of the materials in use are circulated back into the economy. What's more concerning is the fact that just two years ago the number was 9.1%.
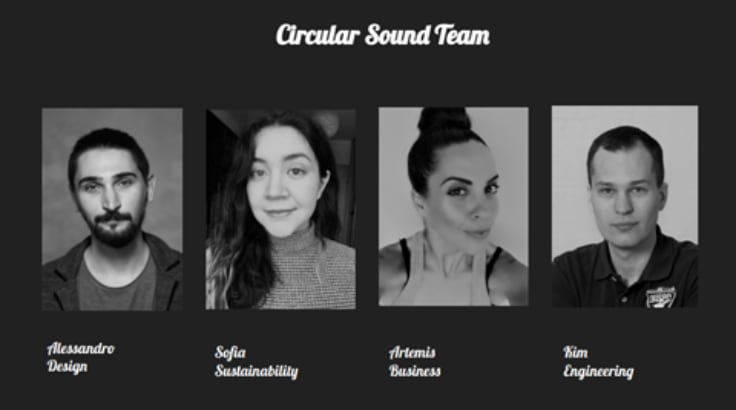
RD Physics, a Finnish startup has identified this issue, and are on a journey to positively impact circularity, starting with the loudspeaker industry. In our conversation with Kim-Niklas Antin (Founder) and Artemis Kloni (Business Analyst), we dive deeper into this problem and understand how they are making loudspeakers circular.
"Developing loudspeakers has been my hobby ever since I was a teenager. I started building my first loudspeakers in the wood shop in school. The results were quite satisfactory, and it motivated me to further develop this industry. I was brainstorming ways of how positive impacts can be made in loudspeakers. The big breakthrough arrived when I participated in an event called Circular Sprint. During this event, we discussed the potential ways of making additive manufacturing circular. That’s when I had the idea of transforming loudspeakers into a fully circular product," began Kim.
Identifying focus area
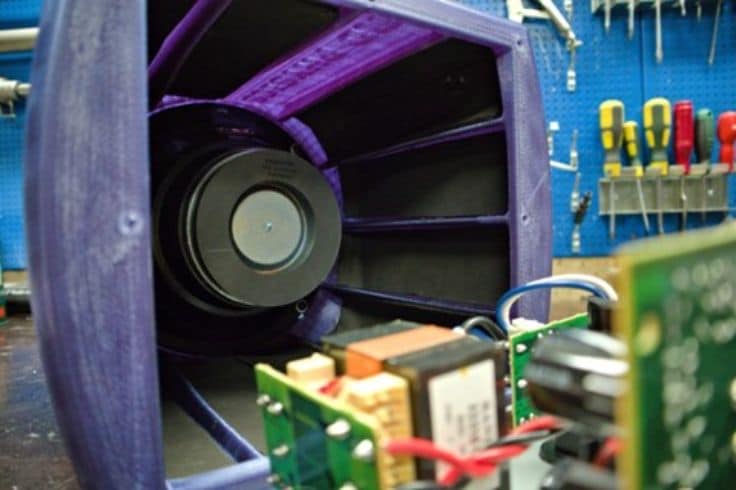
Kim kicked off his venture by analyzing the enclosure of loudspeakers and thought about suitable manufacturing methods. Eventually, he realized that the problem was in fact in the components. The magnets in loudspeaker transducers contain a lot of rare earth elements, sourced from China. The pandemic lead to significant supply chain issues and shortages. Magnets find applications in many industries, including renewable energy and automotive and events like pandemic can disrupt the supply chain. In order to tackle shortages in the future, he came up with a plan to ensure steady supply of materials.
"Our idea was to keep magnets and other components in circulation, by sourcing it from old loudspeakers and putting them into a remanufacturing loop. Remanufacturing involves disassembling used loudspeakers for its components and use it into a new product," continued Kim.
Remanufacturing with 3D printing
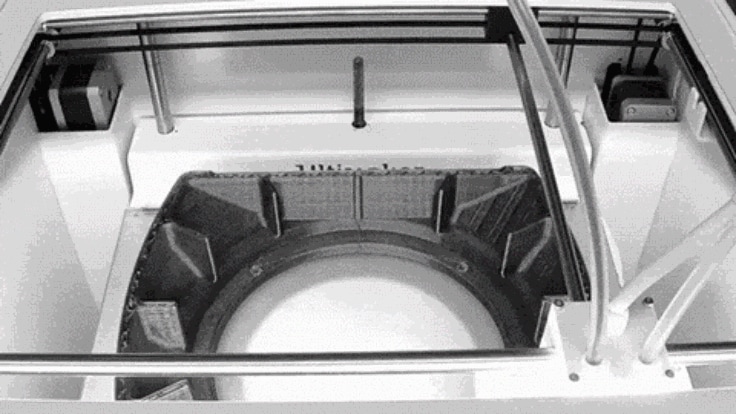
The solution offered by Kim and his team uses 3D printing for facilitating remanufacturing. The new loudspeaker would be reassembled with salvaged components from old loudspeakers, with a new 3D printed enclosure. They call this project ‘Circular Sound’ and it involves remanufacturing using drivers and electronics from discarded speakers with a 3D printed enclosure out of either recycled or bio-based material.
"At the moment, we have a digital business model, where we enable our customers in assembling loudspeakers themselves by providing them with readymade digital prints of the final product. We want to educate a wider audience on the benefits of additive manufacturing and how it can close the manufacturing loop. We provide our customers ready-made 3D prints files and technical know-how of speaker assembly, thus promoting circularity in the sound industry," added Artemis.
Operating in a niche market
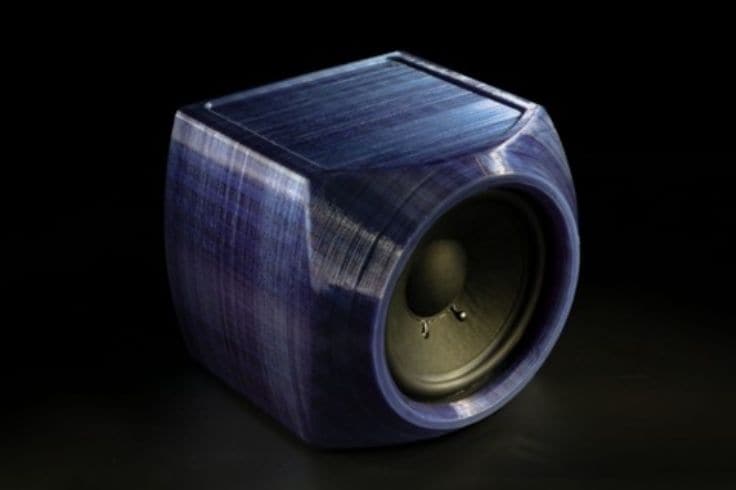
The scale up strategy identified by the RD Physics team focuses on sustainable design and outsourcing manufacturing by collaborating with local printing hubs. The manufacturing process for complex geometries makes a stronger case of 3D printing for their project. "We have already identified users who are more sensitive towards sustainability and circular economy as early adopters. During our market research and promotional campaigns, we realized that our target market is quite niche. It belongs with people who are more environment conscious and are willing to try new sustainable products," explained Artemis.
"Our long-term vision is to raise awareness about the issues related to virgin material to promote remanufacturing. We want people to experience joy of building something themselves, like the IKEA model. The satisfaction of building your own product indirectly translates to longer lifetime for the product," concluded Kim.