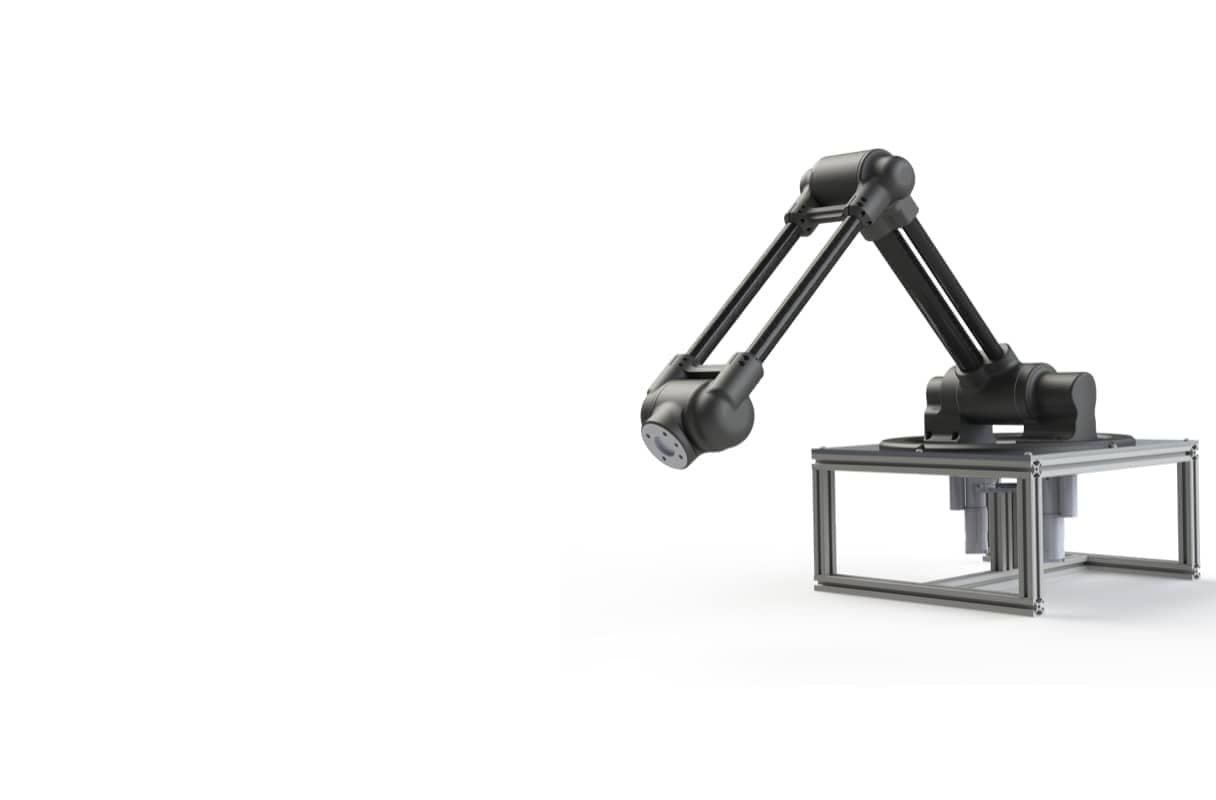
Lunar Rover Arm
Mitsubishi Chemical Advanced Material’s startup accelerator, Growth Garage concluded the High-Temperature Carbon-Fiber 3D printing challenge in December 2021. In this challenge, the participants were asked to incorporate the strength and properties of the KyronMax® carbon-fiber 3D printing filament with the flexibility and sustainability of 3D printing in their design. The challenge focused on three main criteria: technical and commercial feasibility, scalability and sustainability. We are composing a series of articles featuring the finalists and winners of the challenge, so that the readers get a comprehensive view about their product, motivation and vision for the future.
Aidan Mitchell & the Concordia University Team: Lunar Rover Arm
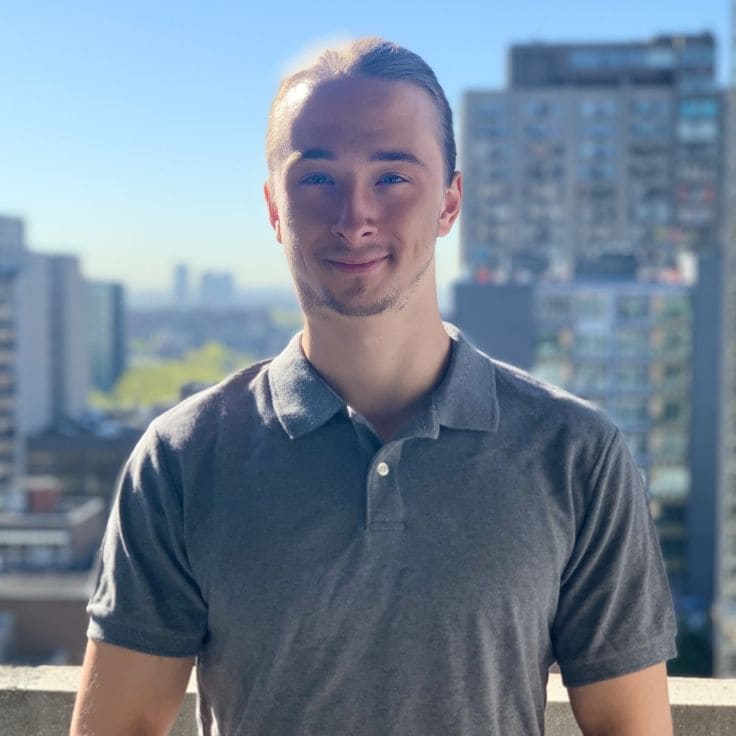
In this second article of our series, we are featuring the Student Award Winners from Concordia University based in Montreal, Canada. The student project is currently being carried out by a group of seven undergraduate students who are developing a robotic arm which would be installed on a lunar rover for excavation and sample collection activities. The project is based on specifications provided by the Canadian Space Agency.
"The parameters that we are dealing with are mainly extreme fluctuations in the ambient temperature on lunar surfaces. We must equip the lunar arm to not only operate in the extreme heat of the lunar day, but also during the extreme cold weather of the lunar night. Our task is to design and manufacture a preliminary prototype which can survive in these conditions," explained Aidan. Additionally, the lunar surfaces also tend to have significant levels of radioactivity. It is imperative to ensure that the lunar arm is protected against these conditions.
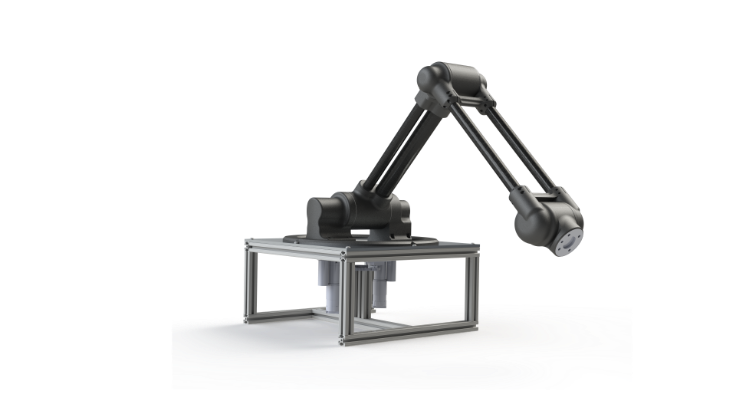
Typically, robotic arms employ motors housed within the arm to provide articulation at several joints. It isn’t feasible to implement this mechanism in environments with extreme temperature fluctuations. In order to protect the electronic components, the actuators and electronics are enclosed inside the insulated and heated enclosure of the rover located below the arm. "To address these problems, we have decided to implement a complete mechanical motion transmission, which allows us to enclose the electronic components such that they don’t get exposed to the surroundings," explained Aidan.
Light, flexible and energy efficient
The scope of activities that would be performed by the lunar arm are restricted to excavation and sample collection. The robot assembly uses a shaft and gear motion transmission, which ensures a smooth mechanical motion. "The base of the assembly is equipped to have five degrees of freedom, which enables the arm to perform 360-degree motions. The second motor moves the top joint, enabling the excavation motion," said Aidan. The lunar arm must be light in order to ensure that the energy spent on its transportation is minimal. At the same time, it should have enough force and lift capacity to be able to collect soil samples.
KyronMax® is perfect for us
"We are opting to use 3D printing, as we want to build prototypes with complex geometries, quickly and economically. When we were conducting the material research, we stumbled upon the 3D printing challenge. After researching more about the KyronMax® material, the team realized that it is perfect for our project. The main value proposition of KyronMax® is its high strength, which makes our task easier of creating a light and strong prototype."
Knowledge and Mentorship
Being the winners of the student award, the lunar arm team would receive support and mentorship from MCAM and Growth garage for design optimization, material selection and creation of business plans. "As students, we are always looking for avenues and opportunities for gaining knowledge, receiving guidance and support from experts in the field. We are really looking forward to working with the MCAM team to steer our project towards the path of success," concluded Aidan.