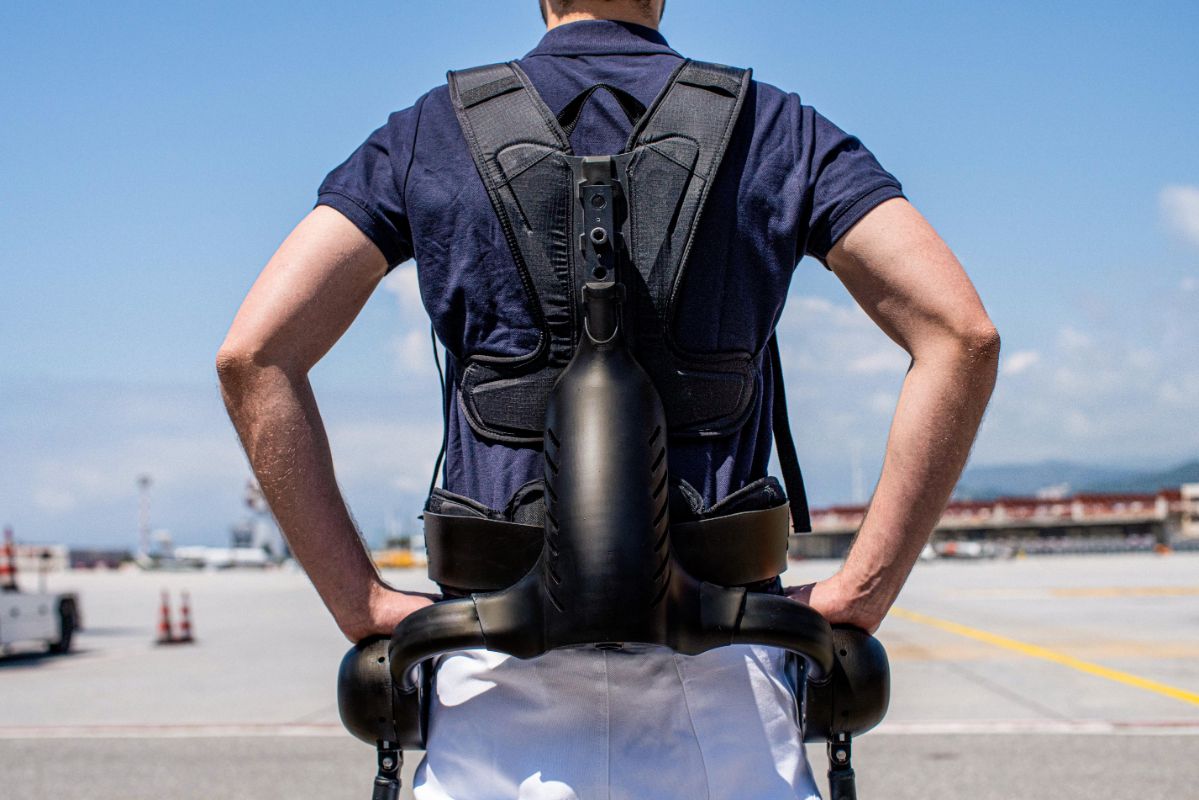
The Movi exoskeleton: Proteso's pursuit of optimizing worker well-being
Lower back pain and musculoskeletal injuries pose significant risks to workers engaged in physical labor and tasks involving manual material handling. These conditions, classified as musculoskeletal disorders (MSDs), originate from the repetitive lifting of heavy objects and physical labor. In the European Union alone, more than 40% of workers suffer from lower back pain annually, primarily due to the strain resulted from manual labor. A majority of these individuals experience physical workloads compounded by tasks requiring awkward body postures and repetitive movements, which contribute to the onset of musculoskeletal injuries.
Source: National Center for Biotechnology Information
Proteso, a startup from Italy is addressing this important issue with their innovation Movi, an electrically powered, back support exoskeleton. Stefano Toxiri, CEO at Proteso shared interesting insights about their product and its journey.
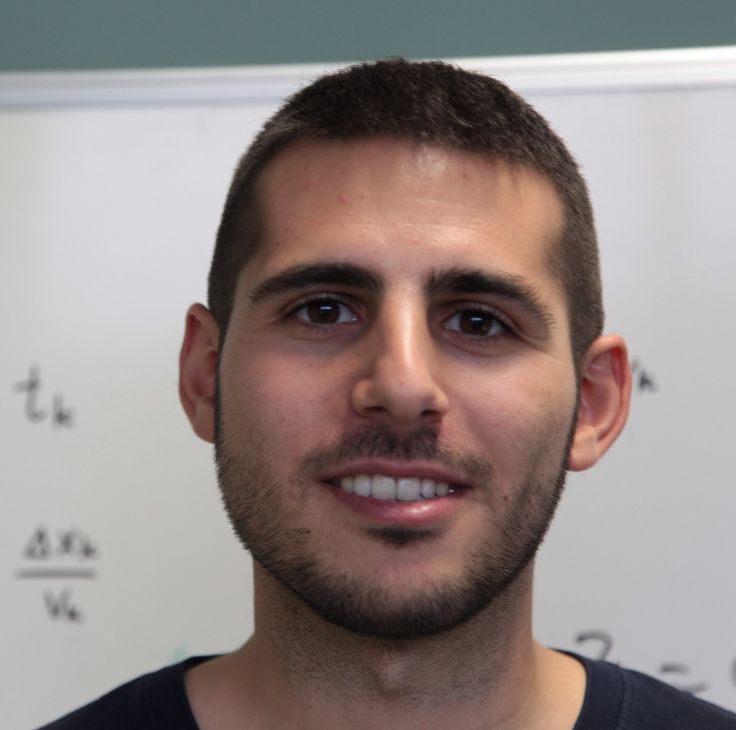
"At Proteso, we're really passionate about what we do. We're a deep-tech startup, and our focus is on developing powered exoskeletons specifically for industrial workers. Our goal is to create wearable technologies that not only ensure safety but also contribute to the overall well-being of workers across different industries. We believe that our products can revolutionize the way companies operate by enabling injury-free productivity and reducing fatigue and pain among workers. We're all about making exoskeletons that are easy to use and comfortable to wear, so they seamlessly integrate into daily work routines," started Stefano.
Proteso originated as a spin-off from the Italian Institute of Technology, where their team dedicated 10 years to intensive research and development within the field of exoskeleton technology. During this period, they carefully designed and iterated multiple generations of exoskeletons, tailoring them for diverse applications.
Movi, the flagship exoskeleton
Movi, developed by Proteso is a powered back-support exoskeleton that provides physical support when lifting and transporting heavy objects, thereby halving the physical strains that lead to back pain and injury, ultimately preventing their onset. By preventing back pain, the quality of life for workers increases, and the costs associated due to reduced productivity and employee turnover is significantly reduced.
"Our product offers superior effectiveness and usability compared to that of competing exoskeletons. We have incorporated sophisticated proprietary algorithms that track and interpret the user’s movements in real time. Built-in sensors recognize activities (e.g., lifting and transporting objects, walking, idling), which triggers the onboard actuators when required. This helps mimic the user behavior and maximizes effectiveness, while simultaneously achieving the most natural user experience possible," continued Stefano.
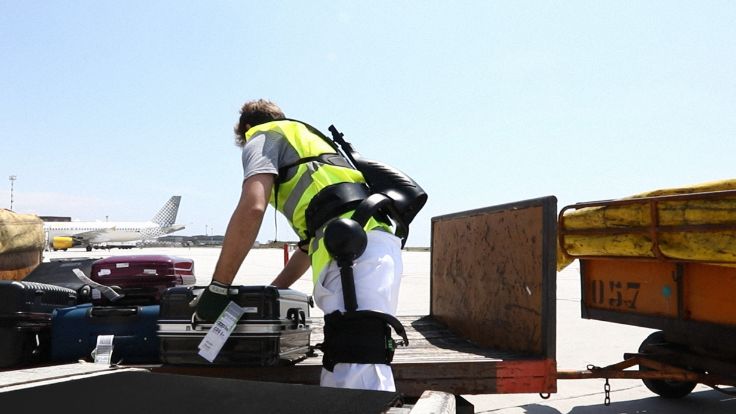
The algorithm has been developed so that users can maintain full control and swiftly adapt to the gentle yet decisive assistance provided by the exoskeleton. It can detect instances of excessive workload and generate warning signals during high-risk postures and periods of exertion.
Data-driven product iteration
The Proteso team have developed a scientific approach called 'Equivalent Weight' that enables users to actively track and measure the functioning of Movi. It was developed in collaboration with the Italian Institute of Technology and the Italian Workers’ Compensation Authority (INAIL). This methodology allows customers to precisely quantify the advantages of integrating Movi into their workflows.
"In addition to the Equivalent Weight approach, we have integrated an advanced data analytics platform into our exoskeletons. This platform is designed to aggregate and present crucial insights derived from exoskeleton fleet data, empowering employers to optimize device deployment, track user movements, and further optimize the workflow," explained Stefano.
Proteso's solution comprises three primary components i.e.
- The hardware which constitutes the core of their offering
- The software which includes their proprietary algorithm for a more user-centric build.
- The cloud which includes a data-analytics platform that measures and relays information to the users
Exoskeletons are technically challenging to build
"At present, the availability of commercially viable exoskeletons on the market is quite limited. One of the primary reasons for this scarcity is the technical complexity involved in their design and construction. While incorporating motors into a wearable frame may seem straightforward, the real challenge lies in ensuring that the exoskeleton is lightweight and comfortable for workers," quoted Stefano.
For exoskeletons, the algorithms plays a central role in determining its effectiveness and functionality. It is important to understand the intricate workings of the human body, the causes of injuries, and translating this knowledge into computationally-efficient algorithms. This process requires a deep understanding of biomechanics and injury mechanisms to ensure optimal performance of the exoskeletons.
"Team Proteso has been developing robotic exoskeletons for workers over the past decade, and we have tested several design and engineering iterations in the process. This has resulted in one of the most advanced exoskeleton technologies in the market," continued Stefano.
3D Printing facilitates frequent, quick design adaptations
Exoskeletons currently operate within a technological landscape that demands ongoing design changes and enhancements. This constant evolution requires manufacturing techniques capable of accommodating such demands. 3D Printing stands out as a solution that offers versatility and agility in facilitating swift iteration cycles. Furthermore, 3D Printing with pellets (FGF) enhances manufacturing capabilities by accommodating a broader range of materials in relatively small batch sizes, allowing for the production of up to 1000 units per year.
"At Proteso, we're not just building products; we're shaping the future of work. We are committed to driving innovation, enhancing workplace safety, and empowering businesses towards creating a better work environment for their employees," concluded Stefano.
Proteso was one of the Finalists in the 3D Printing FGF Engineering Challenge. The jury team was impressed with their unique product addressing the significant issue of repetitive load lifting and its adverse long-term effects.